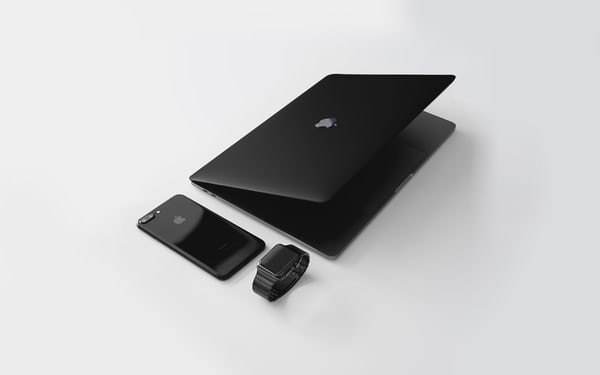
How Apple creates ingenious products
From idea to testing and product release
Idea development
All of Apple’s great products are born in one of the company’s most secretive divisions, Industrial Design (ID).
It’s a group that works directly with Johnny Ive, Apple’s chief design officer. The members of the ID team formulate a request: we want this kind of product. For example, we want to make glasses which allow people to see at night, and are this big, and not too heavy. Then they pass this request on to Product Design (PD), who look at how to implement the request and pass the smaller tasks on to other departments: mechanics, acoustics, surface specialists, and others. They do not know the whole task because of the high level of secrecy, but study in general terms what the device should do and the current capabilities of the hardware.
Within a month, the PD gets a response from each of the teams–for example: “yes, we can do it, it will take two months” – and gives it to the ID. Designers from the Industrial Design team discuss the further solution together with Tim Cook and Marketing, who confirms that they have analyzed the market and can offer it a new product.
Only if ID and Cook say yes, does the company take the risks and start spending resources. This is how the HomePod, iPhone, and every other device the company has created.
Developing prototypes
When the management agrees on a project, all the specialists who will develop the product need access to study secret documents.
The team also receives a list of strict deadlines: on such and such a day of such and such a month, proto1 must be ready, then two months later proto2, etc. From this point, the responsibility of the Directly Responsible Individual (DRI) – the person who is directly responsible for the work – starts. His task is to find contractors, give them an order, control the timing, etc.
After that, you can move on to building prototypes.
Each product has three prototypes, within which 100 to 500 devices are built. The first prototypes are always built in Cupertino. Once they are approved, most of the team gets on a plane and flies to China, where they work out every step from building the line to programming the robot doing the assembly. Apple does not own the factories, but fully owns the structure.
After all the prototypes in the penultimate construction phase, the team actually has the final recipe for creating the product, a complete set of information, an active team, and an estimated release date.
Deadlines are taken very seriously. Of course, there can rarely be a shift in deadlines, but overall the company works like clockwork – everything is very coordinated.
Testing
After the first prototypes are created, the team prepares a specification by which they will test the development from the bolt to the final product. The testing is in progress. They put a camera in the iPhone, they test it.
The complete cycle of project development can take from 1 to 5 years, depending on its complexity. There are, of course, longer projects which Apple has not even announced yet.
Testing of the final product is handled by a special team, which is responsible for reliability. They receive the device and for a few weeks they influence it in every possible way: they throw it in water, wash it in a washing machine, dry it in a dryer, throw it against walls. After all the crash tests, they write a report for the team: for example, they need to increase the strength of the screen.
At one of the final stages of testing, employees with a certain level of access can get a product to wear secretly. A prototype is created that looks like a last-generation device, but has new stuffing. The employee uses it in normal life, can take it outside the company.
I’ve experienced it myself. Once, I noticed that one of our speakers had an operating system on his phone that looked a bit off. He did not show it on purpose, I noticed it casually in conversation. A few months later Apple released an update and only then did I realize that it was a test copy.